The Benefits of Shibaura Machine’s Proprietary Injection Molding Servo Motor and Ball Screw Design
ELK GROVE VILLAGE, IL, September 17, 2021 - As the technology for injection molding machines continues to evolve, all-electric has become an increasingly popular option. When it comes to comparing and choosing the right all-electric machine for your factory, looking into the design of the servo motors, amplifiers, and ball screws is critical. When well-engineered, these components can greatly increase the benefits of lower energy costs, improved consistency, and reduced cycle times.
Shibaura Machine's long history in the machine tool industry has given us the opportunity to develop key proprietary technology in servo motor and ball screw design. These crucial components have been designed by our team specifically for all-electric injection molding machines, nothing coming “off the shelf”. Here is what molders should know about the unique design of Shibaura Machine’s servo motors, amplifiers, and ball screws.
Unique Servo Motor Technology
As a leader in developing energy-efficient machines, Shibaura Machine’s SXIII series synchronous servo design allows for a more eco-friendly, quieter, and faster operation with improved repeatability. Several highlights include:
- Maintenance free
- No power used when idle
- High torque at low and high speed
- No cooling fans required as standard
- Dynamic braking
- Rare Earth magnets hold position when there is no power
Ball Screws Designed for Injection Molding
The design of the ball screws is essential to ensure precision and longevity of this key component. Shibaura Machine designed the ball retainers to reduce wear and increased runs of the balls transfer load over a greater area.
This allows for retainers to assist in holding lubrication, improved durability and efficiency because of less friction between balls, and reduced noise levels due to the retainers stopping rolling ball impact.
Learn More
Contact the injection molding team at Shibaura Machine to learn more about these unique features of the SXIII series today.
Contact us today to see if our SXIII series can help your molding shop achieve its goals!
Related Articles View All Articles
Mold Deflection Causing Problems With Your Injection Molding Process? Read This.
ELK GROVE VILLAGE, IL, September 9, 2021 - When it comes to manufacturing plastic parts to tight tolerances, minimizing mold deflection is essential. Mold deflection is generally caused by clamping and cavity pressures which then cause the mold to deflect ...
Read moreOptimize Part Weight Consistency with the Shibaura Machine Plastrol Function
ELK GROVE VILLAGE, IL, September 2, 2021 - Part weight variations due to inconsistent check ring response can cause unwanted fluctuations and endanger a stable injection molding process. When we look for ways to stabilize the process and improve shot-to-sh...
Read moreShibaura Machine’s New Smart Factory Highlights IoT Solutions Paired With All-Electric Injection Molding Technology
ELK GROVE VILLAGE, IL, August 27, 2021 - Shibaura Machine will be launching its new Smart Factory with an open house at their Elk Grove Village, Illinois tech center in the Fall, 2021. This manufacturing cell will further support customers to fully leverag...
Read moreTaking LSR Molding to a Higher Level with All-Electric Technology
ELK GROVE VILLAGE, IL, August 20, 2021 -Liquid silicone rubber molding is experiencing demand growth like never before in North America. While many manufacturers are considering whether to invest in a dedicated liquid silicone rubber (LSR) molding machine...
Read moreTwo-Shot Molding: Any Machine, Any Time with Shibaura Machine
ELK GROVE VILLAGE, IL, August 6, 2021 - Two-shot molding is one of the most efficient processes for manufacturers creating products using plastics. By allowing operators to create multi-material or multi-colored parts without adding extra assembly steps it...
Read moreInjection Molding Energy Consumption At a Glance
ELK GROVE VILLAGE, IL, July 28, 2021 - From energy hogs forty years ago to the efficient all-electric options of today, injection molding machines have made quite the evolution. While injection molding is still an energy intensive process, the all-electric...
Read moreWant to know more about our machines?
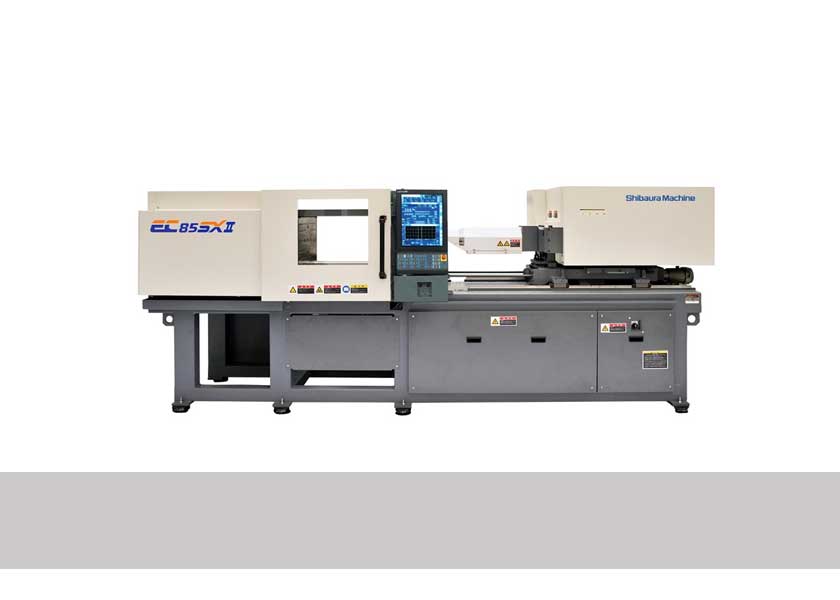
Injection Molding Machines
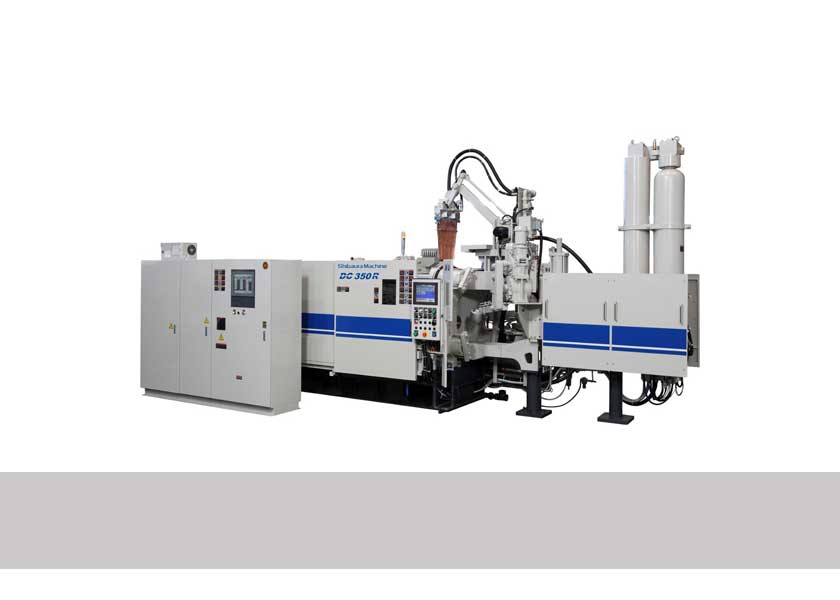
Die Casting Machines
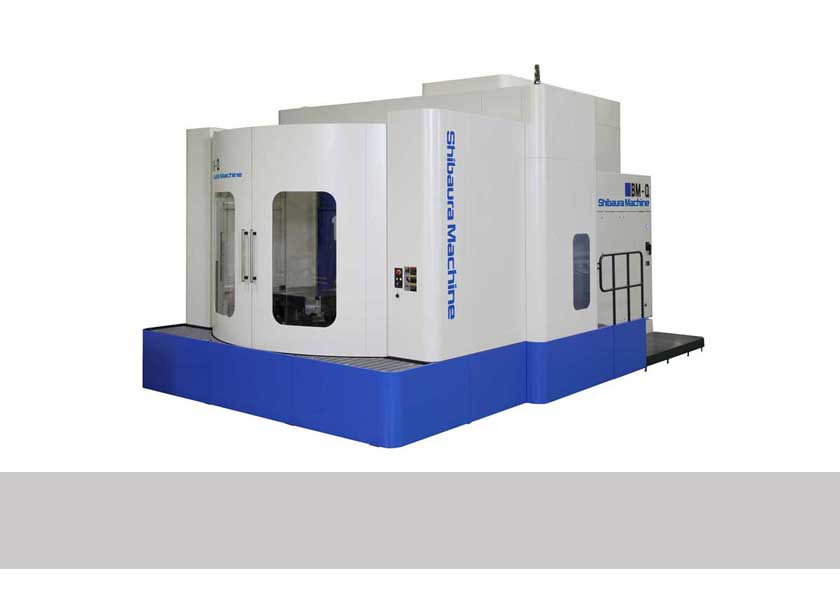
Machine Tools
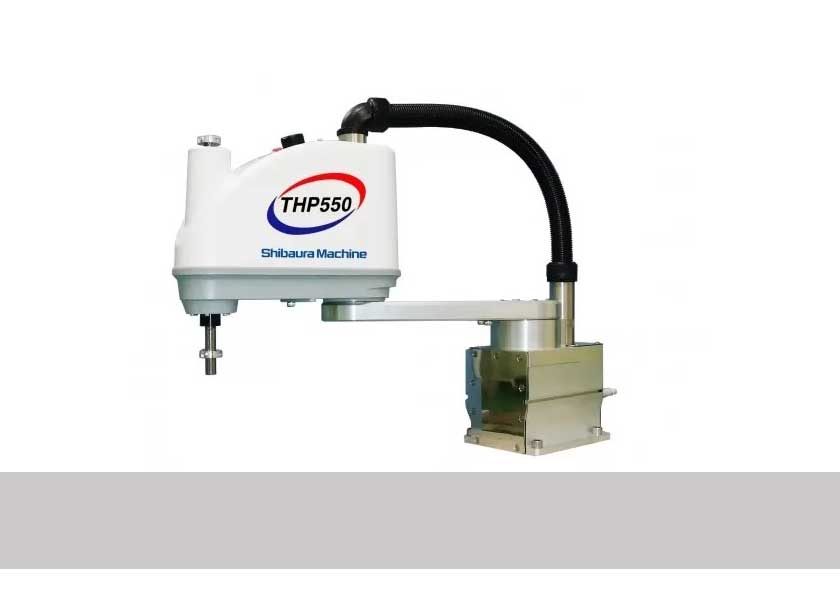