Looking to Reduce Scrap? Why All-Electric Injection Molding Machines Are the Clear Choice
ELK GROVE VILLAGE, IL, January 12, 2022 - Improving scrap rates in injection molding can have a large impact on increasing profitability. While there are many process improvements for scrap rate reduction, it is also important to consider the type of machine doing the job. To achieve consistent scrap rate improvement and become more competitive, many manufacturers are now moving away from hydraulic and choosing to invest in all-electric technology.
Challenges with Hydraulic Machines
Although hydraulic machines are still a popular option, when it comes to repeatability, a major factor in scrap rate reduction, these machines simply can not match that of all-electric.
Compared to their all-electric counterparts they consume a large amount of energy- even when idle. In order for the hydraulic machine to move it also requires a combination of hydraulic oil, valves, hoses, manifolds, pumps, and hydraulic cylinders. The performance and wear of these components create increased opportunities for process variations, which can impact part quality.
Maintaining proper oil temperature is also critical for molding success with hydraulic machines. Hydraulic machines use heat exchangers which must be cooled using chiller or tower water and risk fluid leakage making them a less than ideal choice for clean room requirements. Variations in water flow or temperature due to scale buildup or contamination of the cooling equipment, pipes, or machine heat exchanger can further negatively affect the process and the part quality.
Improve Repeatability, Reduce Scrap Rates
Powered by independent CNC servo motors, all-electric machines offer a combination of tighter precision, higher predictability, and consistent repeatability. This results in many benefits, but most notably reduced scrap rates.
The electric servo motors, ball screws, and linear guides are perhaps the biggest benefits these machines have over hydraulic when it comes to reducing scrap rate. Using a servo motor and ball screws for each movement on the Shibaura Machines ECSXIII series allows for the improved positioning accuracy and increased repeatability compared to hydraulic machines. The linear guides for movement of the injection and moveable platen that the ECSXIII machines use also make them an excellent choice for clean room applications. The tie bar bushings found on hydraulic machines need lubrication, introducing grease into the molding area that can often contaminate parts.
All of this also adds up to the all-electric machines offering better performance and productivity.
Learn More
Contact the Injection Molding team to discuss how the precision, repeatability, and cleanliness of the ECSXIII series offers a much larger processing window enabling you to significantly reduce your scrap rate.
Tel: (888) 593-1616
Contact us today to learn how our all-electric technology can help your team reduce scrap rates!
Related Articles View All Articles
Faster Cycle Times with All-Electric Injection Molding
ELK GROVE VILLAGE, IL, January 6, 2022 - Considering changing out from hydraulic to all-electric machines in the new year, but trying to justify the change? Look no further than the improvements these machines can make to your cycle time. Being able to red...
Read moreHow Automatic Load Cell Calibration Helps Prevent Molding Defects
ELK GROVE VILLAGE, IL, December 29, 2021 - One of the key advantages of all-electric injection molding machines is the ability to monitor actual plastic pressure during injection via a load cell behind the screw, without the need for in-mold transducers. ...
Read moreHow the I/O Checker Minimizes Machine Downtime for Injection Molders
ELK GROVE VILLAGE, IL, December 21, 2021 - Creating injection molded parts not only requires a high level of technical expertise, but also attention to detail. One small mistake can slow down, or even stop production.How many times this year have machine d...
Read moreHow the Mold Guide Makes Set-Up Simple and Efficient
ELK GROVE VILLAGE, IL, December 16, 2021 - Installing a mold in an injection molding machine is a routine process. However, even when tasks are routine, mistakes can be made. Being able to perfect mold change-overs and lessen mistakes can not only help imp...
Read moreShibaura Machine is Making It Simple to Minimize Injection Molding Defects
ELK GROVE VILLAGE, IL, November 30, 2021 - Small mistakes in injection molding can add up to costing companies big money when it comes to time and product lost. Understanding design guidelines and best practices help in preventing defects, but not all mold...
Read moreSupporting Our Southeast Injection Molding Customers: Spotlight on Shibaura Machine’s Charlotte, North Carolina Tech Center & Service Office
ELK GROVE VILLAGE, IL, November 19, 2021 - This is our last week in our Injection Molding Support Series, focusing on our Charlotte, North Carolina facility. While Shibaura Machine operates in a truly global network, these four locations throughout North A...
Read moreWant to know more about our machines?
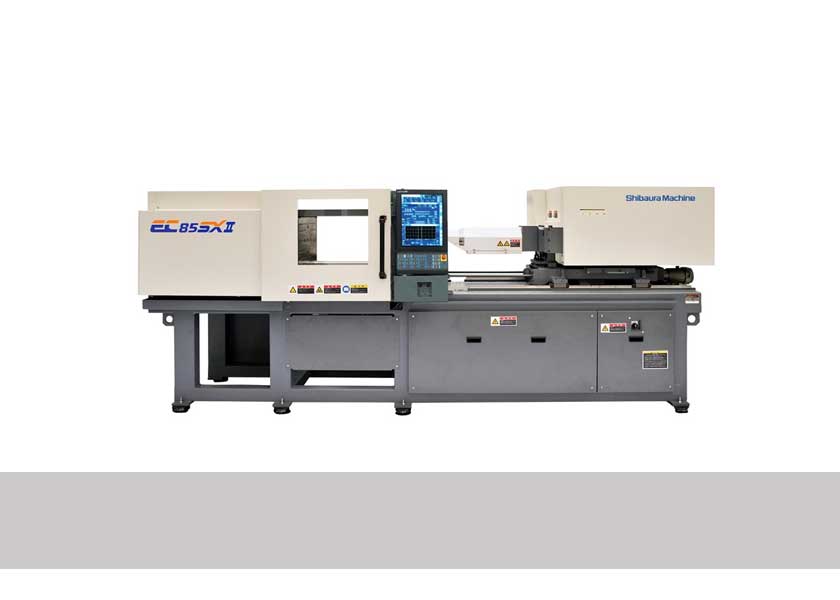
Injection Molding Machines
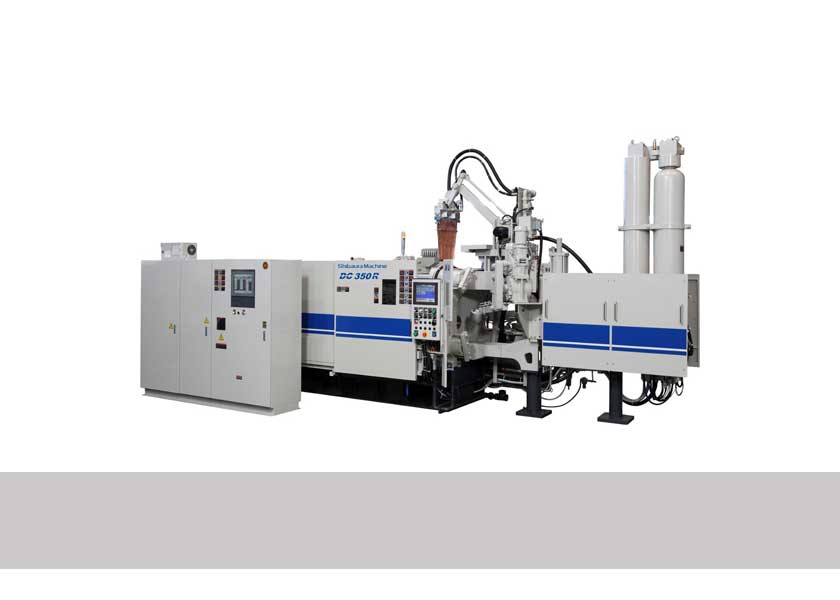
Die Casting Machines
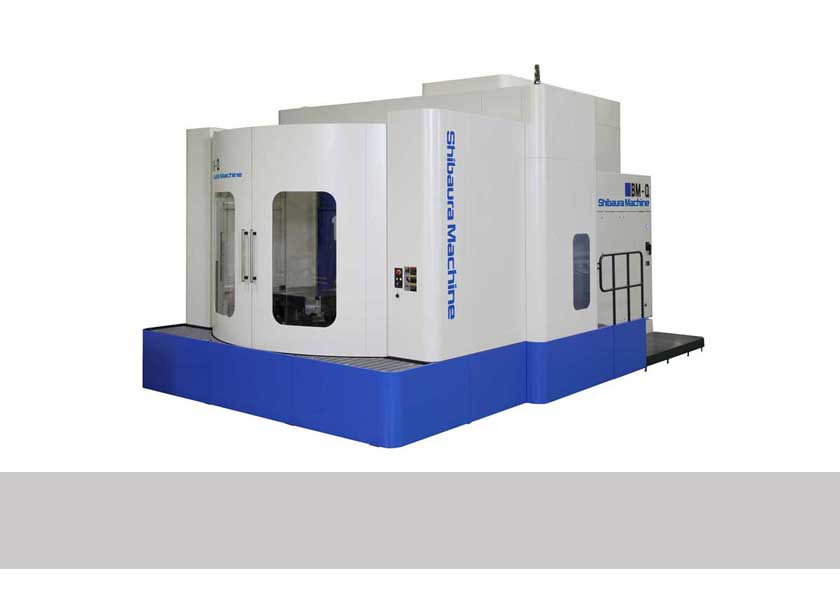
Machine Tools
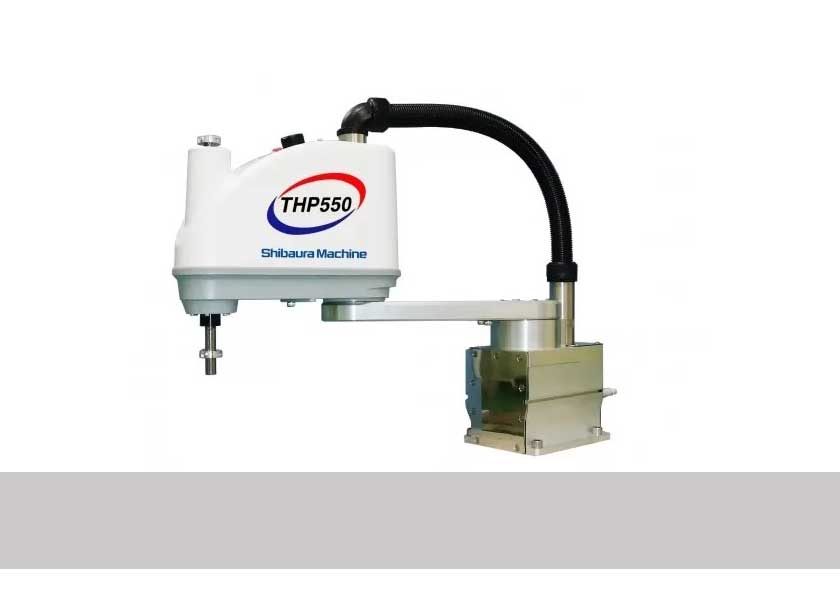