4 Ways to Ensure Precision Filling Transfer Using Final Pack Control
ELK GROVE VILLAGE, IL, March 24, 2022 - The more you can control your production conditions in injection molding the more repeatable your results. When it comes to transfer from the filling stage to packing it might be considered the most crucial element of the entire molding process to control in order to maintain high-quality, precise repeatability in part production.
In order to achieve an optimum packing process, the transfer from the filling stage needs to be repeatable. Shibaura Machine’s Final Pack Control (FPC) function on the V70 controller allows the processor to control which method of transfer they require. This function allows the user to specify limit values or allows the machine to dictate values in order to ensure the pressure does not exceed set limits after the mold has been filled and that no damage is done to the mold or injection molding machine.
Four Options for Timely Transfer
The FPC function has four different selections a processor can make in order to switch from speed to pressure control. Ultimately, all of these functions are designed to finish packing out the part by holding a constant pressure for a set amount of time to produce an ideal fit, form, and functional quality part that meets the dimensional requirements per the quality standards of that part.
The most common option is to transfer by position, known as LS4 on the controller. This allows the user to set a position to have the machine move from the filling stage to the packing stage at the given set point. LS4 is particularly useful when thin-walled parts are being produced because the pressure profile and time can be specified to ensure limits are not exceeded. Without controlling this process, high-pressure peaks can occur and potentially create costly damage to the mold and machine.
Depending on the material, part weight, or dimensions the user may also choose another option for final packing control.
- Transfer by injection pressure
This option allows the user to input a set injection pressure within a range of screw positions that the machine will switch from the filling stage to the packing stage once it reaches that set pressure. Switchover by pressure can alleviate sink marks in the finished part (pressure too low) or over-packing (pressure too high).
- Transfer by cavity pressure
Users may choose this option when a mold/tool is instrumented with cavity sensors and the user can switch from the filling stage to the packing stage based on the actual cavity pressure within the tool.
- Transfer by an external signal
Users are able to transfer from filling to packing stage based on an external signal from a third-party monitoring system of the user's choice to fulfill their needs.
Start Improving Productivity and Cost Efficiency
At the end of the day, the transfer from filling to packing needs to be repeatable. The more the user can control the transfer, the better likelihood for increased productivity and improved part quality. Contact the Injection Molding team to learn more about how the Final Pack Control function on the V70 Controller can help your shop start improving cost-efficiency.
Tel: (888) 593-1616
Contact us today to learn how Final Pack Control can help improve your molding process!
Related Articles View All Articles
How to Establish Optimum Fill Time with Precise Control
ELK GROVE VILLAGE, IL, March 16, 2022 - When it comes to injection molding, the filling stage is critical. Filling too fast in order to save time or reduce the process cycle can end up causing gas to become trapped in the vents. Filling too slowly or fast ...
Read moreImprove Product Quality with Better Screw Speed and Back Pressure Control
ELK GROVE VILLAGE, IL, March 9, 2022 - When it comes to improving part quality and cycle times, don’t underestimate the power of proper control of back pressure and screw rotation. Together, these two functions have a major influence on an injection moldin...
Read moreImprove Injection Molding Part Weight Stability with Plastrol
ELK GROVE VILLAGE, IL, March 2, 2022 - Many manufacturers are facing increased supply chain hiccups, especially when it comes to resin. Pair that with increases in demand for everything from medical devices to semiconductor components and this leaves littl...
Read moreMinimize Your Footprint and Bring Precise Control with Hot Runner Integration
ELK GROVE VILLAGE, IL, February 23, 2022 - Hot runner technology has revolutionized the injection molding process since it was introduced over 50 years ago. With it, manufacturers have seen improved molded part quality, operational efficiency, and reduced ...
Read moreMonitor Injection Molding Energy Consumption Easily on the SXIII Series
ELK GROVE VILLAGE, IL, February 16, 2022 - Plastic injection molding machine drive technology has evolved dramatically over the decades. One of the most significant changes is the all-electric servo drive design in comparison to traditional hydraulic machi...
Read moreReduce Cooling Water Load with All-Electric Machines
ELK GROVE VILLAGE, IL, February 2, 2022 - Water cooling systems have long been used in hydraulic injection molding machines in order to keep the machine running smoothly. But imagine being able to reduce cooling water load requirements- it will allow you t...
Read moreWant to know more about our machines?
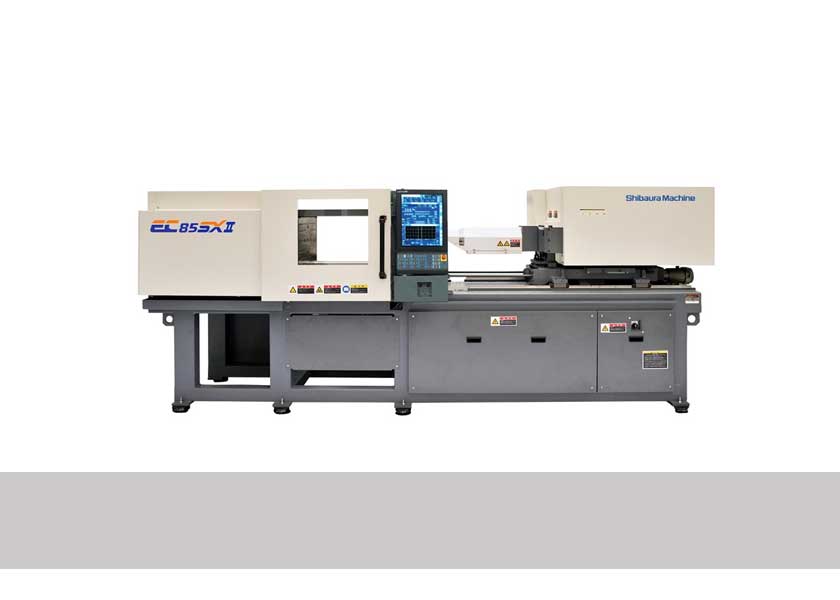
Injection Molding Machines
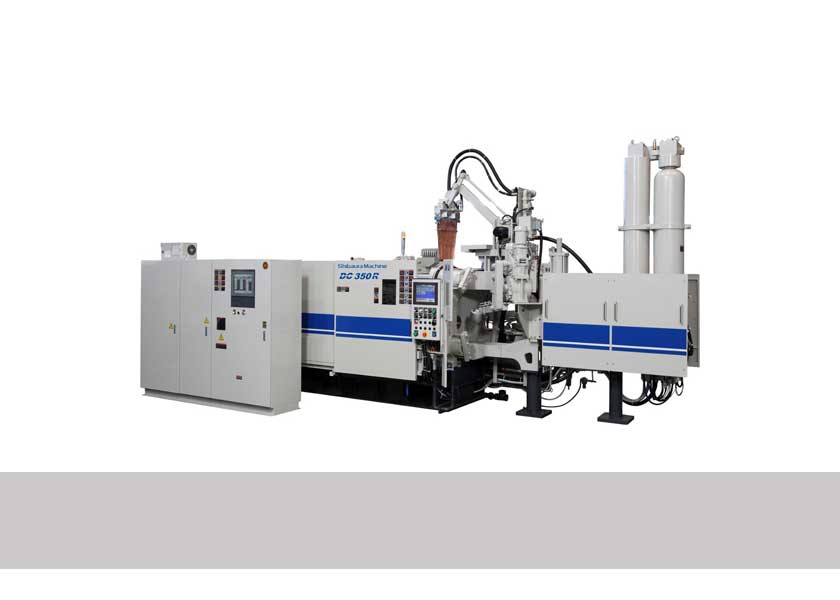
Die Casting Machines
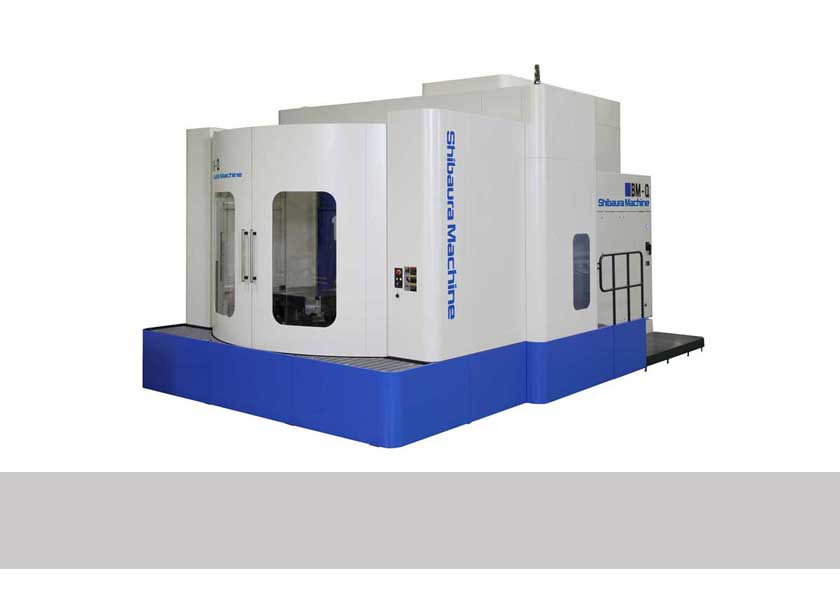
Machine Tools
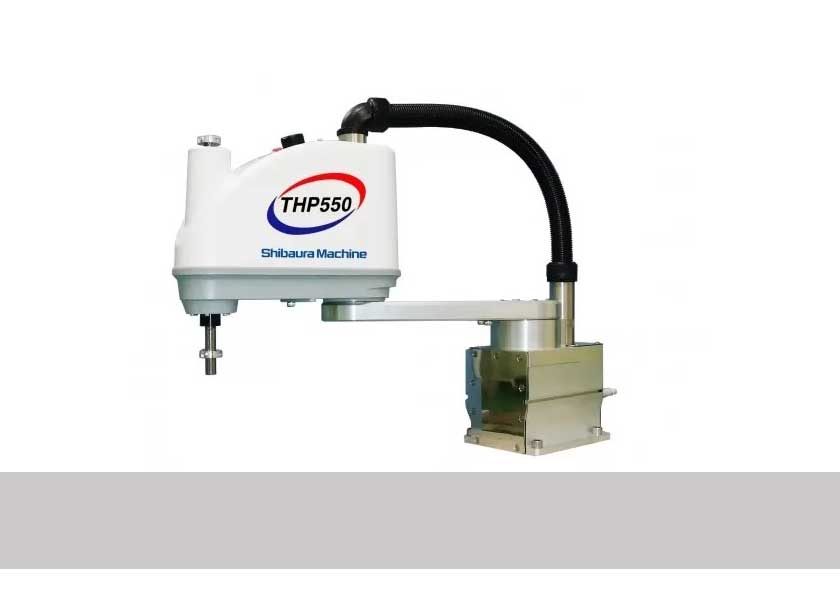