5 Ways to Reduce Injection Molding Start-Up Scrap with Shibaura Machine’s ECSXIII Series
ELK GROVE VILLAGE, IL, July 15, 2021 - When it comes to improving your injection molding process, reducing scrap at machine start-up is one of the more effective ways to increase efficiency. With costs rising on materials and shortages throughout the industry, optimizing your start-up processes in order to reduce scrap will not only improve production efficiency but decrease your carbon footprint and the associated costs.
The SXIII injection molding machine by Shibaura Machine allows manufacturers a solution to reducing start-up scrap with five easy to use features. By focusing on controlling scrap, manufacturers can better focus on remaining competitive and maximizing their benefits.
SXIII Injection Molding Machine Features to Reduce Scrap
In order to offer an easier and more effective solution for the reduction of start-up scrap, the team at Shibaura Machine designed these features within the SXIII technology:
- Dry Cycle Mode: This function is selectable with one button. The machine will run in dry cycle mode to ensure mold movements are correct to minimize start-up cycle interruptions.
- Dynamic Self Tuning (DST) Press: To ensure the correct tonnage is applied as the mold expands due to thermal expansion, the DST-Press function is put in place. This control allows for the strain gauge on the tie bar to measure actual clamp tonnage and the machine can adjust on-the-fly to maintain the proper tonnage to eliminate short shots and improve venting during start-up.
- Start-Up Feature: This easy to navigate interface allows users to utilize a soft start program and have it act consistently. Users can pre-set a certain number of shots at start-up where the machine injects at a lower speed, position, and pressure, while gradually ramping up to production settings. This allows the process to stabilize while minimizing the amount of start-up scrap.
- Auto Purge: Ensure the material is ready for production by eliminating black specks and degraded material by running the auto purge program prior to start-up. Users can set up this feature to run at the end of production and/or before a new production run.
- Back Pressure in Manual Mode: This feature helps eliminate the potential for human error and inconsistency, while ensuring the back pressure in auto remains at the right parameter. There is a separate screw back pressure setting for manual mode. This prevents the user from having to change the production back pressure setting for manual purge and having to remember to put it back before running automatic, thereby preventing potential start-up scrap parts.
Begin Reducing Start-Up Scrap Today
It is worth your time to take a close look into these features to ensure you are experiencing as few inefficiencies as possible. If you don’t currently operate the SXIII injection molding machine and are working towards improving quality and efficiency throughout your facility, contact our team to learn more about how this equipment can help.
Contact us today to learn how our ECSXIII series can help you reduce start-up scrap!
Related Articles View All Articles
From One Product to the Next- Improving Set-up Efficiency in Injection Molding with SMED and the SXIII
ELK GROVE VILLAGE, IL, July 7, 2021 - Reducing the changeover time for your operations is critical to maintain a competitive advantage and improve profitability in the manufacturing industry today.That’s where the concept of single-minute exchange of die, ...
Read moreGain Control Over Your Barrel Temperature with Shibaura Machine’s V70 Controller
ELK GROVE VILLAGE, IL, June 25, 2021 - Errors in temperature control result in a large part of rejects in the injection molding world. If a molder wants to ensure a stable molding cycle and high quality product, having a temperature control process is esse...
Read moreUsing Auto-Purge to Improve Injection Molding Efficiency
ELK GROVE VILLAGE, IL, June 23, 2021 - Molders today are always looking for a way to minimize their losses. So while purging is often necessary, it makes many molders cringe because this process often means costly waste and lost production time- defeating...
Read moreMold Recipe Management: Saving Time and Money in Injection Molding
ELK GROVE VILLAGE, IL, June 9, 2021 - Think of a chef on a Friday night at a popular restaurant. They are tasked with switching from one recipe to the next in a single night. Not only that, they need to make sure they use the correct measurements, with qui...
Read moreInjection Molding Production Management Made Easy
ELK GROVE VILLAGE, IL, June 4, 2021 - Does your injection molding machine offer easy to use onboard production management tools?Many injection molding machines lack user-friendly onboard production management functions. A quality production management tool...
Read moreReducing Cycle Times in Injection Molding: How All-Electric Has Changed the Game
ELK GROVE VILLAGE, IL, May 27, 2021 - Why is reducing cycle times such a popular topic in injection molding? Largely because from both a time and cost standpoint the effects of even a few seconds improvement on your cycle time can have a major impact on yo...
Read moreWant to know more about our machines?
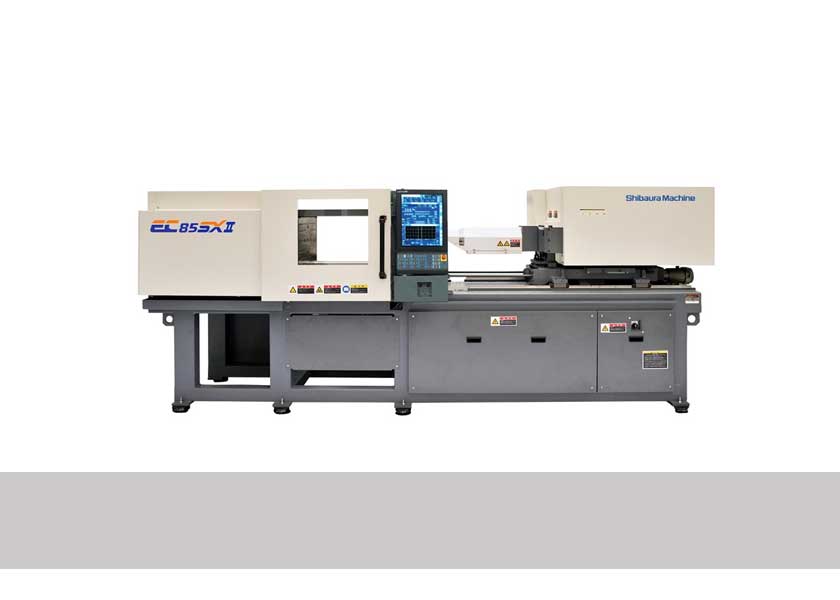
Injection Molding Machines
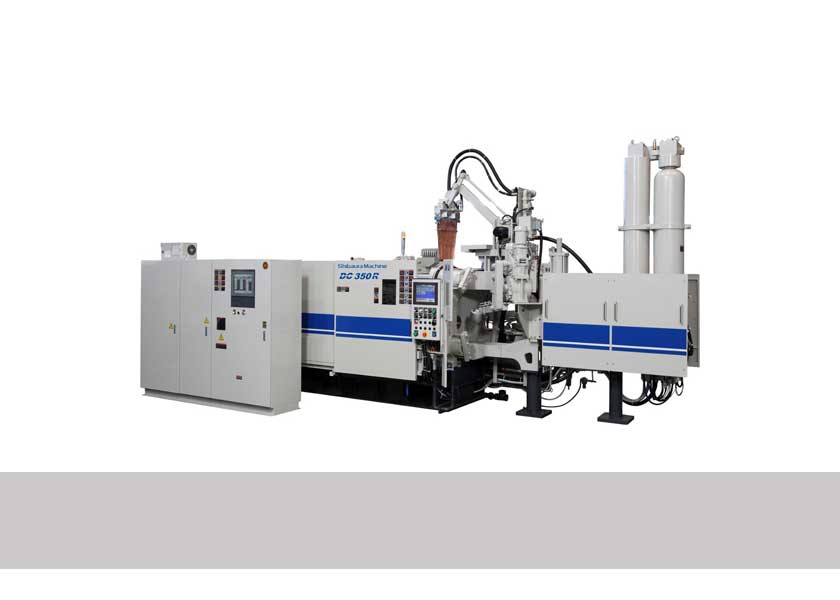
Die Casting Machines
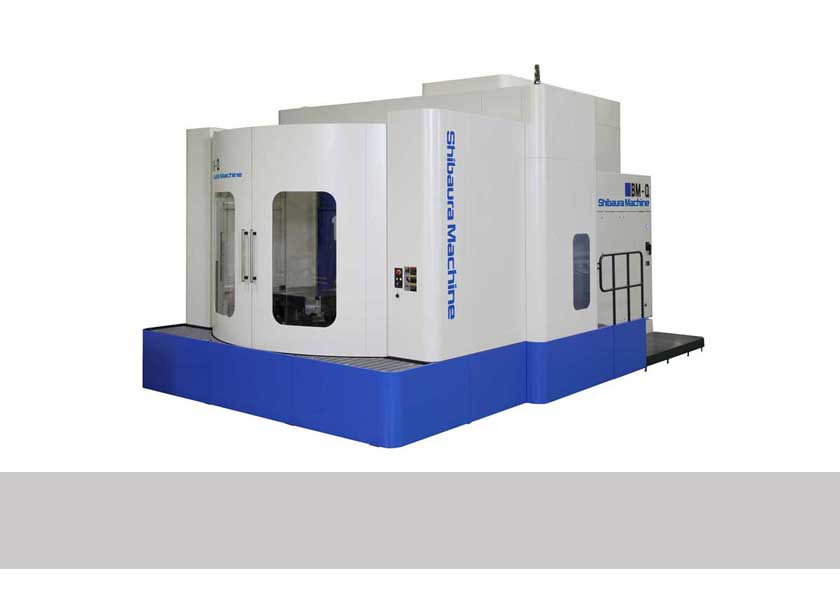
Machine Tools
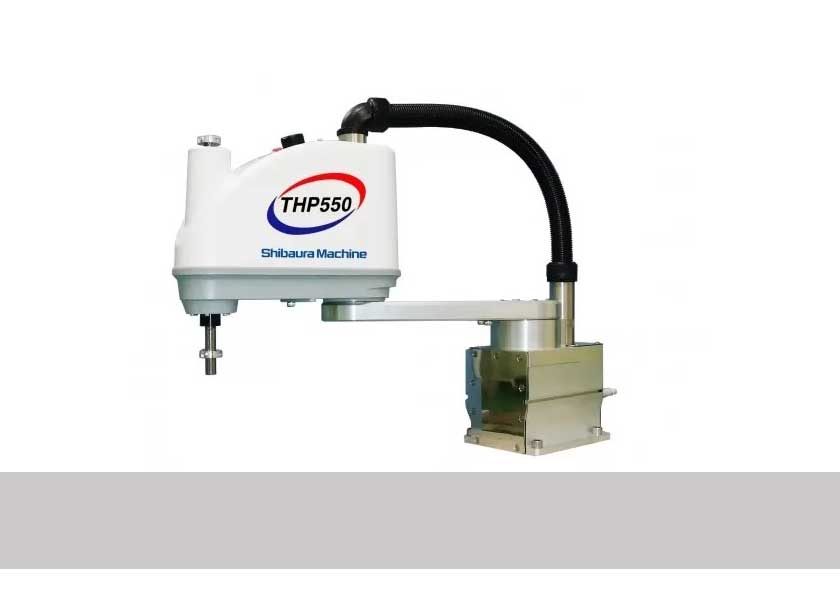