All-Electric Injection Molding Machines Offer More Than Energy Savings
ELK GROVE VILLAGE, IL, February 3, 2021 – Did you know energy spending in most injection molding plants is one of the highest costs month after month? At the end of the day, it is often costing more to run old machines then it would to invest in new, energy efficient ones.
With the evolution in injection molding machines (IMM) over the past couple of decades it is worth exploring machine options and how they can lower energy spending because doing so can make a considerable impact.
Cost Savings Compared
With the strides the technology has taken over the years, all-electric injection molding machines have the opportunity to be upwards of 80% more energy efficient than their old hydraulic predecessors. Beyond optimum energy savings, Shibaura all-electric machines also bring technological advances and efficiency that servo-hydraulic and hybrid counterparts simply can’t compare to such as:
- Increased productivity and repeatability with faster cycle times
- Higher precision means lower scrap rate
- No heat exchangers resulting in lower cooling water requirements
The tables below show an actual Shibaura Machine customer comparative of their existing European 400 Ton servo hydraulic machine against their new EC390SXIII series all-electric machine. As you can see, not only is energy savings obtained, but significant material and productivity gains are also realized.
Bottom line, all-electric machines are the most efficient option on the market today. Compared against servo-hydraulic machines the savings in electricity consumption offers up to 50% with all-electric machines.
Exploring IMM Technologies and Energy Usage
Remember to research the all-electric machine to ensure it is 100% all-electric. While machines with electric main axes can call themselves “all-electric” it doesn’t mean their other functions (ejectors, nozzle forward, etc.) are electric. A truly all-electric machine like the Shibaura Machine SXIII series will have all machine axes electric and offer the optimum in energy savings and precision.
To discuss more detailed information about energy efficient injection molding processes or to request an energy audit for your injection molding machines please contact our team of experts below.
Contact us today to see if our all-electric technology can help improve your bottom line!
Related Articles View All Articles
Improve Quality Control and Productivity with the iPAQET Remote Data Management System
ELK GROVE VILLAGE, IL, January 27, 2021 – Not all monitoring and data management systems are created equal. Many systems are prone to errors, have less than easy to use interfaces, or require someone to be in front of the machine- oftentimes collecting dat...
Read moreHow to Minimize Injection Molding Machine Downtime
ELK GROVE VILLAGE, IL, January 19, 2021 – Whether planned or unplanned, machine downtime is very costly. Aside from directly impacting production and labor, machine downtime extends to other areas of operation and can affect the organization as a whole. An...
Read moreReducing Reject Rates for Injection Molding is Within Reach
ELK GROVE VILLAGE, IL, January 13, 2021 – If parts are considered defective they are likely getting rejected by customers. That means the cost lands on you, but with a premium because you have equipment and labor costs tied into it. Luckily, the right inje...
Read moreReducing Injection Molding Cycle Times Using All-Electric Technology
ELK GROVE VILLAGE, IL, January 5, 2021 – When it comes to improving manufacturing processes, optimizing the parameters of your injection molding machine is critical. Specifically, working to reduce cycle times in injection molding can allow you to produce ...
Read moreEvolving with Our Injection Molding Customers through Superior Support
ELK GROVE VILLAGE, IL, December 29, 2020 – Making an investment in an injection molding machine is as much about the people behind it as the machine itself.Having a true partner that works to find ways to minimize downtime, improve efficiency, and keep you...
Read morePut Our Injection Molding Expertise to Work for You
ELK GROVE VILLAGE, IL, December 23, 2020 – Navigating a challenging year meant adapting new ways to serve customers for many industries. For manufacturers, it meant figuring out ways to increase plant efficiencies and optimize their current processes. Havi...
Read moreWant to know more about our machines?
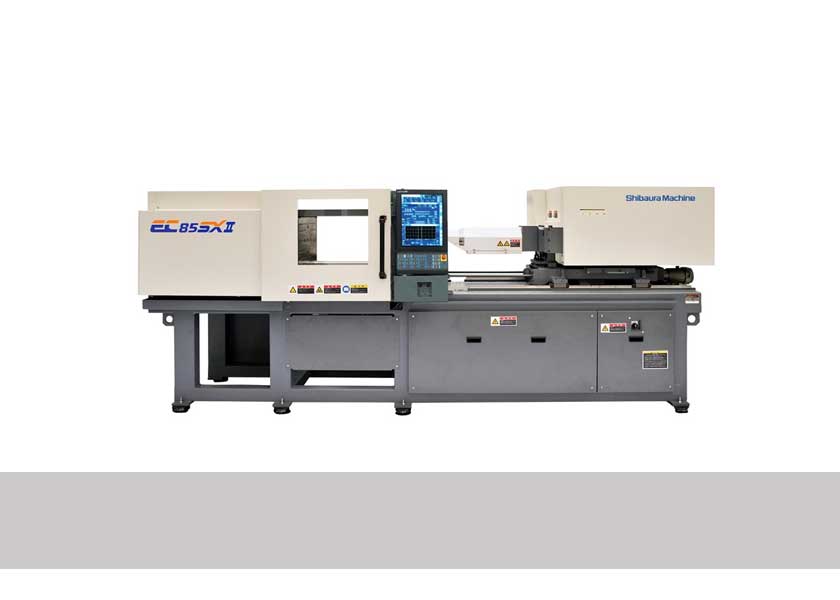
Injection Molding Machines
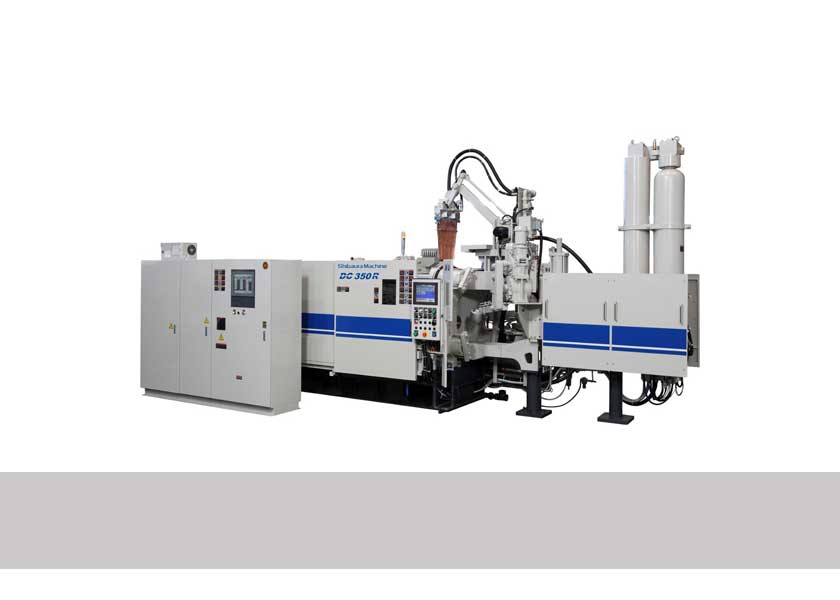
Die Casting Machines
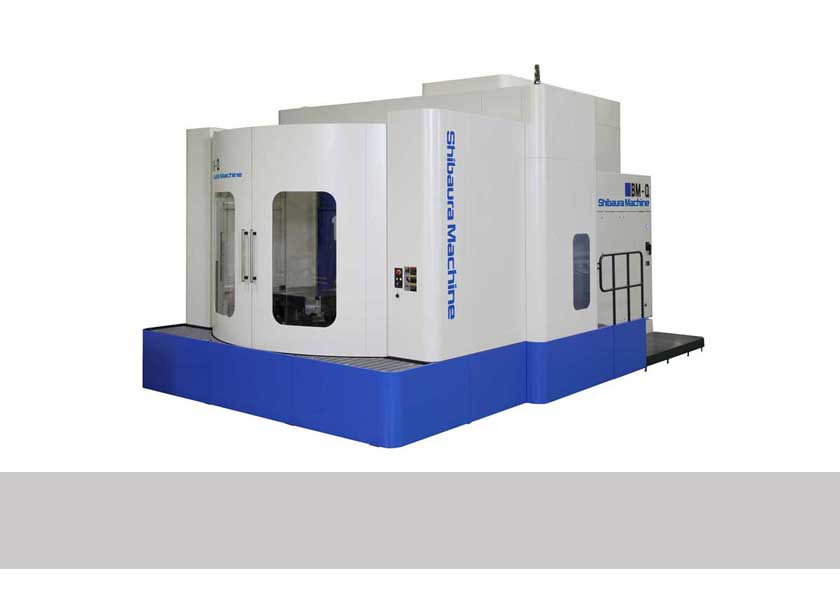
Machine Tools
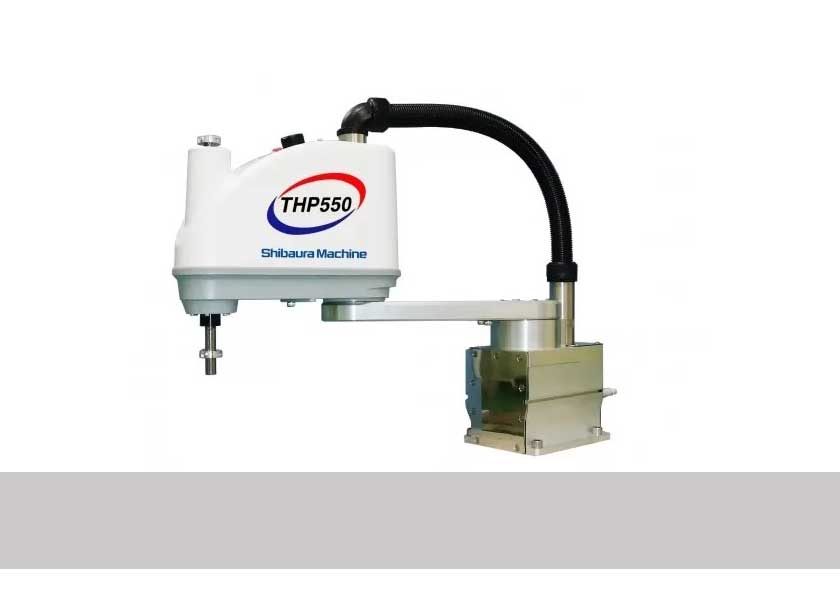