Why Screw Design is Critical to Your Injection Molding Success
ELK GROVE VILLAGE, IL, March 9, 2021 – The proper selection of your screw for any given injection molding application is critical to successful processing. In fact, changing to an optimized screw design has been shown to improve cycle times and reduce part reject rates- all equating to more efficient processing performance.
How can you know you are selecting the proper screw design? When it comes to injection molding you should first consider your application, as some screw variations will allow for superior processing results over others. We are sharing insight into several commonly used screw designs and what applications they are generally used for.
Screw Design Makes a Difference
As mentioned, a specific screw design can be used to enhance performance and even solve processing problems. Several of the most common screw designs to consider include:
General Purpose
Used often because of their highly flexible nature, general purpose screws can be used with most plastic materials. They are a common choice for companies that mold a variety of different materials.
- The single flight screw design works well for most crystalline and glass-filled materials.
- A dynamic barrier general purpose screw design offers a better color mixing ability and ensures a more homogenous melt. This design works well for polycarbonates and clear materials.
High Performance Olefin
Consider a high performance olefin screw when you need enhanced level of melt control. Designed specifically for polypropylene and polyethylene, the high performance olefin screw design provides the fastest recovery time and uniform melt.
Mixing
Mixing screws achieve uniform color, viscosity, and isothermal melt quality while maintaining optimal melt temperature and offer distributive mixing of the melt. Mixing screws allow you to avoid dead spots or hang-up areas that may cause thermal degradation or discoloration.
Additional Applications
Shibaura Machine offers a variety of screws for additional applications. These can include LSR, PVC, and PTFE.
The screw material should also be considered in line with your screw design. With some resins you will want to consider abrasion/chemical resistant or hardened materials to protect from excessive wear.
Choosing the right injection screw allows you to make quality parts consistently and with maximum production output. Shibaura Machine developed its injection molding machines with screws designs that allow for consistent end-product quality, along with high performance and wear resistance.
Contact us to learn more about the optimum screw design for your application.
Contact our processing experts today to discuss the proper screw design for your application!
Related Articles View All Articles
What to Know When Deciding Between All-Electric and Servo-Hydraulic Injection Molding Machines
ELK GROVE VILLAGE, IL, March 2, 2021 – Precision and repeatability. These are two things that all shop floors are looking to continually achieve. When considering what type of injection molding machine you want to help you achieve these things there are se...
Read moreDoes Your Injection Molding Machine Offer Easy Visibility into Diagnostics and History?
ELK GROVE VILLAGE, IL, February 23, 2021 – Troubleshooting and maintenance can become tedious and time-consuming tasks on the manufacturing floor. What would it mean to your business if you were able to more efficiently understand your machine and have qui...
Read moreWhy Injection Molding Machine Design Matters - And What to Look For
ELK GROVE VILLAGE, IL, February 19, 2021 – When you have a well-designed injection molding machine there are no limits to what types of molded parts you can create. Whether it's automotive, packaging, medical, or custom plastics - an injection molding mach...
Read moreMinimizing Injection Molding Complexity without Compromising Capability
ELK GROVE VILLAGE, IL, February 10, 2021 – The convenience of your injection molding machine controller correlates directly with your factory production efficiency. A controller that is not only powerful but offers intuitive operation, simple navigation, ...
Read moreAll-Electric Injection Molding Machines Offer More Than Energy Savings
ELK GROVE VILLAGE, IL, February 3, 2021 – Did you know energy spending in most injection molding plants is one of the highest costs month after month? At the end of the day, it is often costing more to run old machines then it would to invest in new, energ...
Read moreImprove Quality Control and Productivity with the iPAQET Remote Data Management System
ELK GROVE VILLAGE, IL, January 27, 2021 – Not all monitoring and data management systems are created equal. Many systems are prone to errors, have less than easy to use interfaces, or require someone to be in front of the machine- oftentimes collecting dat...
Read moreWant to know more about our machines?
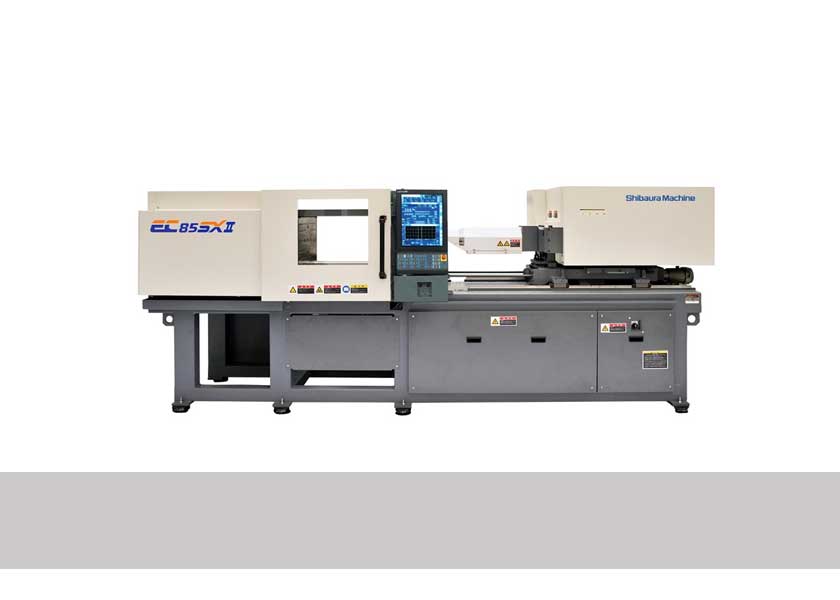
Injection Molding Machines
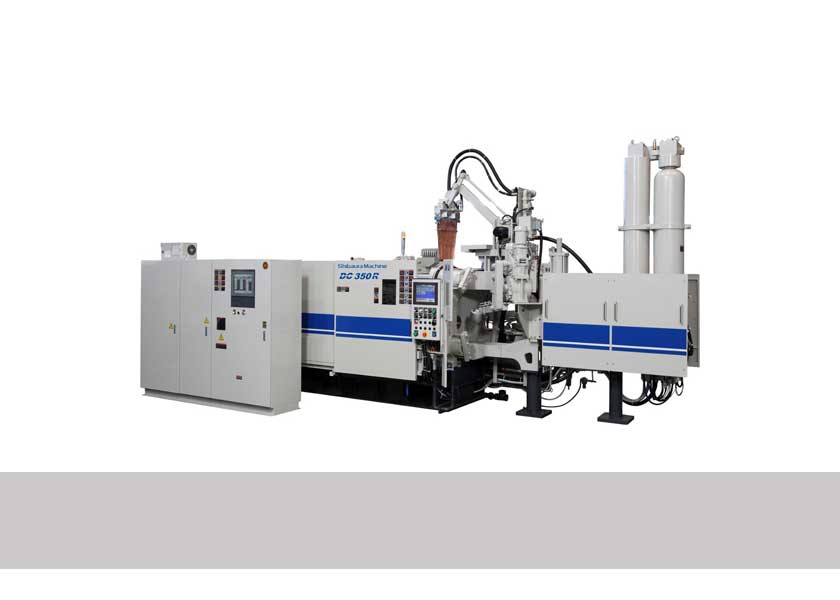
Die Casting Machines
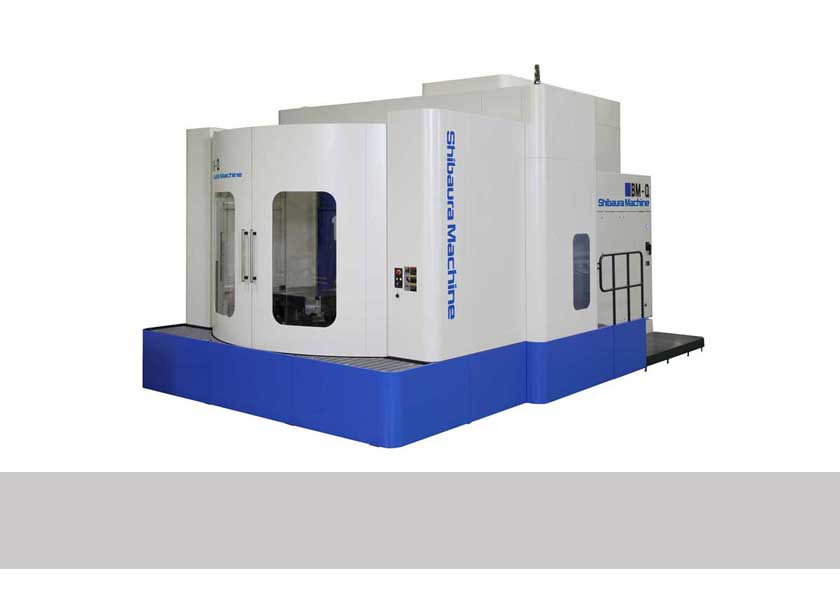
Machine Tools
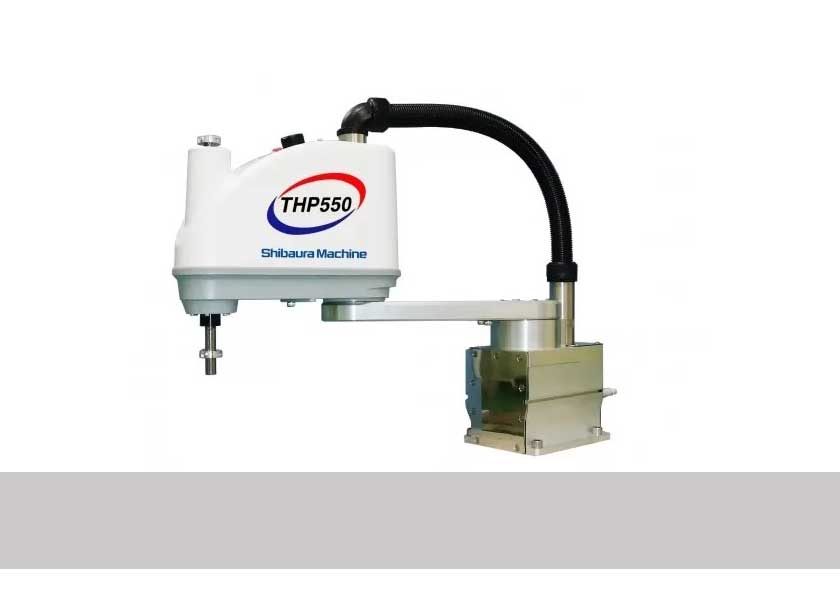